Produkcja w Europie przez wiele dekad nie opłacała się niemal każdej branży, nie tylko tej z przemysłu wysokiej techniki. Obecnie produkcja chipsetów w Europie według przedstawicieli Intela to koszt od 40 do 50% większy w Europie niż w innych rejonach. To stan, który utrzymuje się od lat, nawet pomimo faktu, że wielu światowych gigantów już dawno temu rozlokowało się chociażby w Malezji. Przejeżdżając między kolejnymi siedzibami fabryk w stanie Penang w Malezji w bliskim sąsiedztwie Intela było chociażby laboratorium AMD, Analog Devices czy Infineon. Wyspa w północno-zachodniej części Malezji stanowi centrum operacji dla gigantów produkcji konsumenckich urządzeń.
Tegoroczny Intel Tech Tour, w ramach którego zostałem zaproszony do Malezji, to druga odsłona imprezy. Pierwsza odbyła się w Izraelu, gdzie Intel zapowiedział inwestycje rzędu 25 miliardów dolarów. Wizyta w Azji Wschodniej także umotywowana była inwestycjami w tamtym rejonie. Przez najbliższą dekadę amerykański producent między innymi procesorów oraz kart graficznych zainwestuje 15,8 miliarda dolarów w rozszerzenie produkcji. Obecnie powstają kolejne kondygnacje budynków, które znacznie rozszerzą działalność Intela prowadzoną tam od ponad 51 lat.
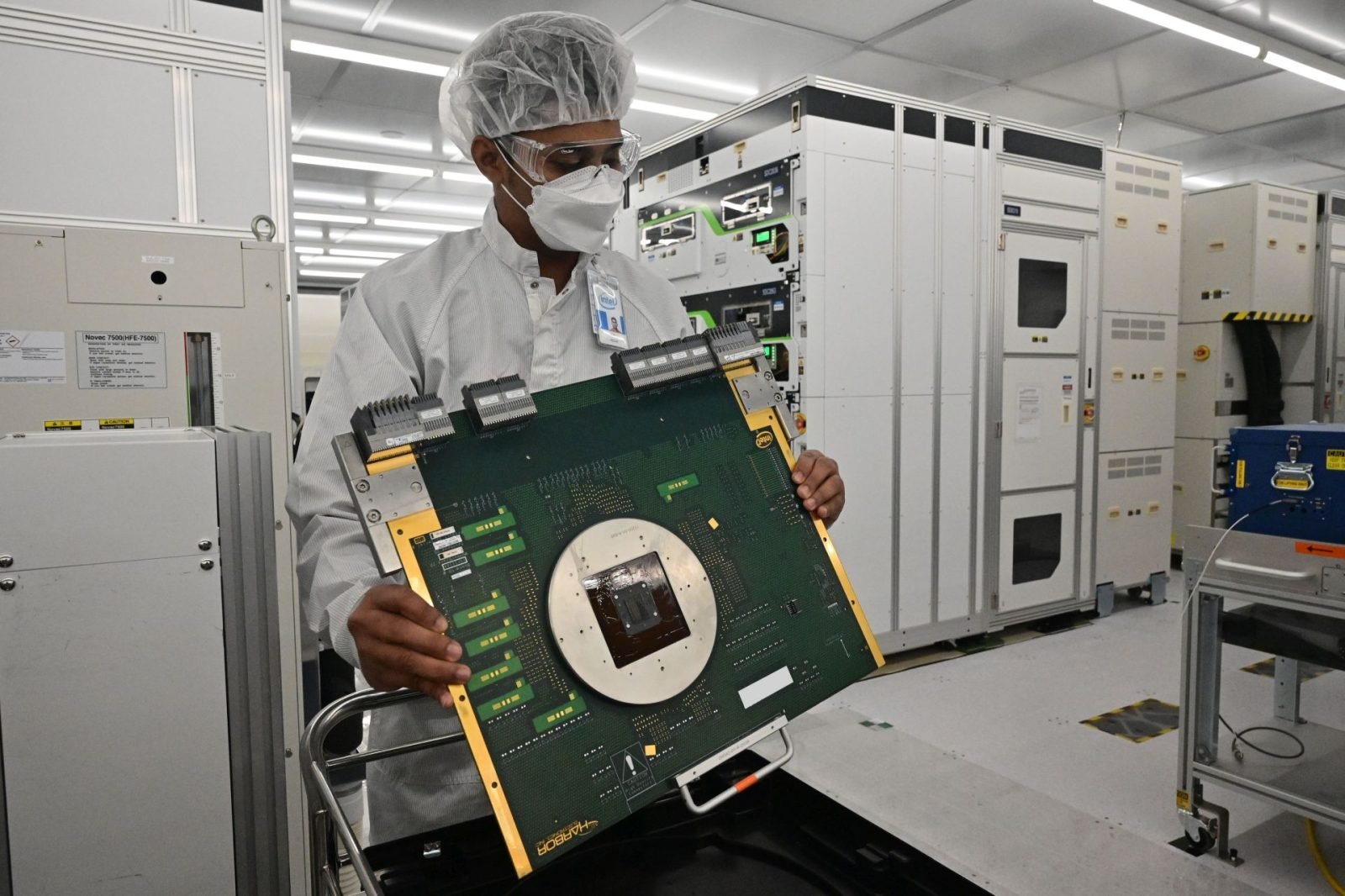
Intel pozwolił mi na unikalny wstęp do centrów produkcji oraz testów najważniejszych komponentów dla współczesnych technologii. Podobna przestrzeń do testowania półproduktów oraz ich składania w końcowy układ jak ta, którą widzieliśmy w Kulim, powstanie w Miękini pod Wrocławiem. Intel Wrocław skontroluje pierwszą partię produktów i złoży ją już w 2027 roku. To proces obwarowany tajemnicami, z których część udało się samodzielnie odkryć, jednak bez własnego aparatu i smartfonu. Jeśli pojawią się tu zdjęcia mojego autorstwa, to pochodzą z przestrzeni, w których przedstawiciele Intela pozwalali nam robić zdjęcia.
Zobacz wideo i zostaw subskrypcję na kanale!
Intel Penang Assembly and Test pozwala wyobrazić sobie to, co będzie działo się w Intel Wrocław
Półprzewodniki wymagają szczególnej troski na każdym etapie produkcji – od formowania wafli krzemowych i ich ubogacania, przez wycinanie z nich płytek, ich bezpieczne składowanie i transport, a następnie implementację na chipsecie. To proces, który jest kosztowny – stworzenie fabryki produkującej wafle krzemowe to koszt rzędu od 10 do 15 miliardów dolarów, a podczas realizacji takiego projektu w różnych etapach powstaje 12000 etatów. Z kolei jedno narzędzie strzelające plazmą do wafli krzemowych w ramach technologii EUV (Extreme Ultraviolet Litography) to koszt 180 milionów euro, a jego przewiezienie do fabryki wymaga pracy 4 Boeingów 747 oraz 35 ciężarówek. Miejsce instalacji wymaga z kolei podniesionych sufitów i wzmocnionych podłóg.
Czytaj też: Półprzewodniki z drewna? To realna perspektywa
To tylko jeden z przykładów, który ma zobrazować, o jak skomplikowanym przemyśle mówimy. Wszystko jest tu podporządkowane temu, by zachować powtarzalność procesu. W Intel Penang Assembly and Test (PGAT), czyli miejscu składania i testowania w stanie Penang, odbywa się kilka czynności jednocześnie.
Najpierw niezbędne są wcześniej wytworzone i wycięte kości, które docierają w formie przypominającej taśmę filmową do fabryki w Penang. Te także wycina się w jednym z laboratoriów Intela w Malezji, choć odbywa się to w Kulim (o tym miejscu później). Pierwszym krokiem w Intel Penang Assembly and Test jest zamocowanie tych kości na podłożach PCB. Po odseparowaniu ich od taśmy trafiają na platformę, gdzie są precyzyjnie umieszczane na podłożach PCB.
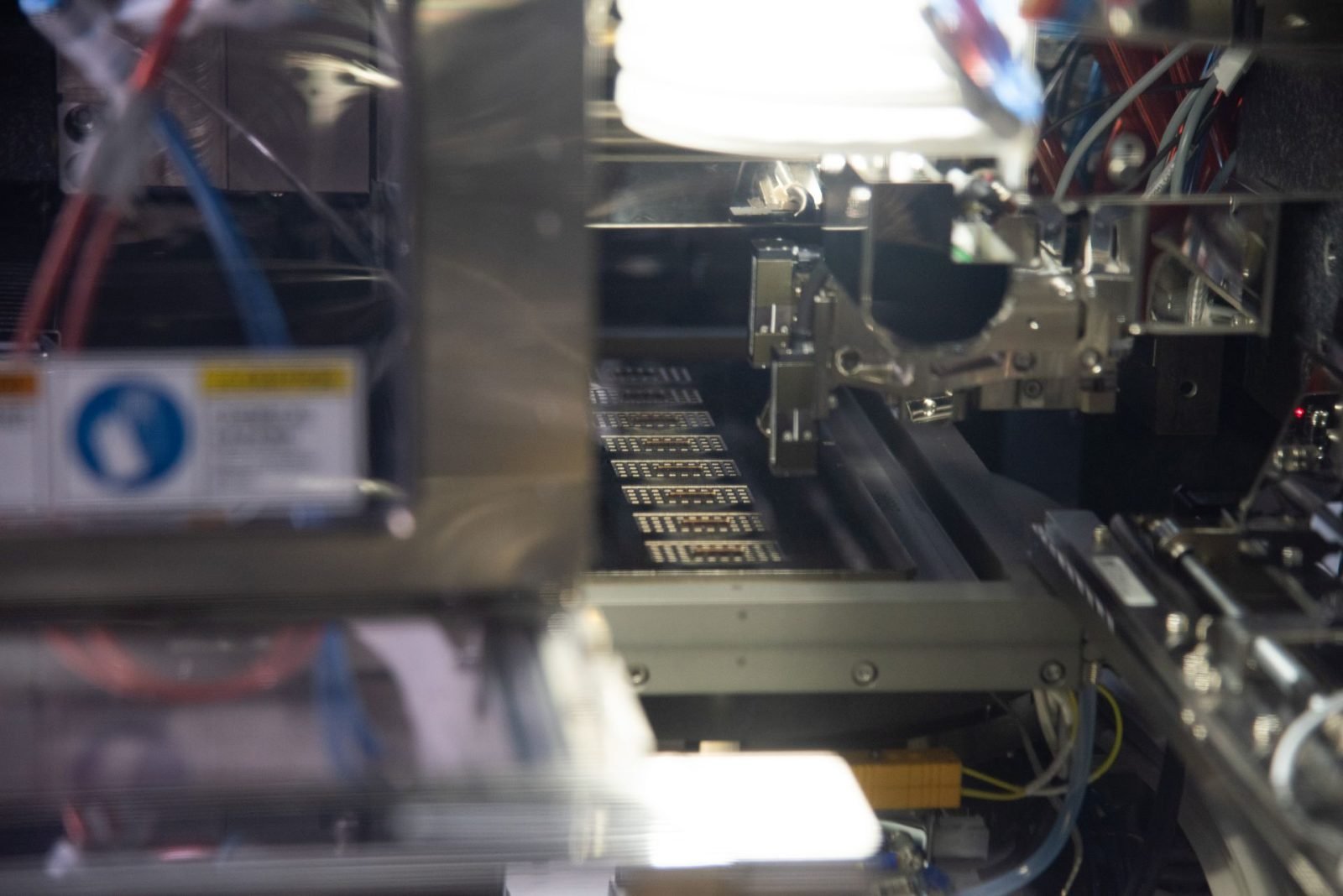
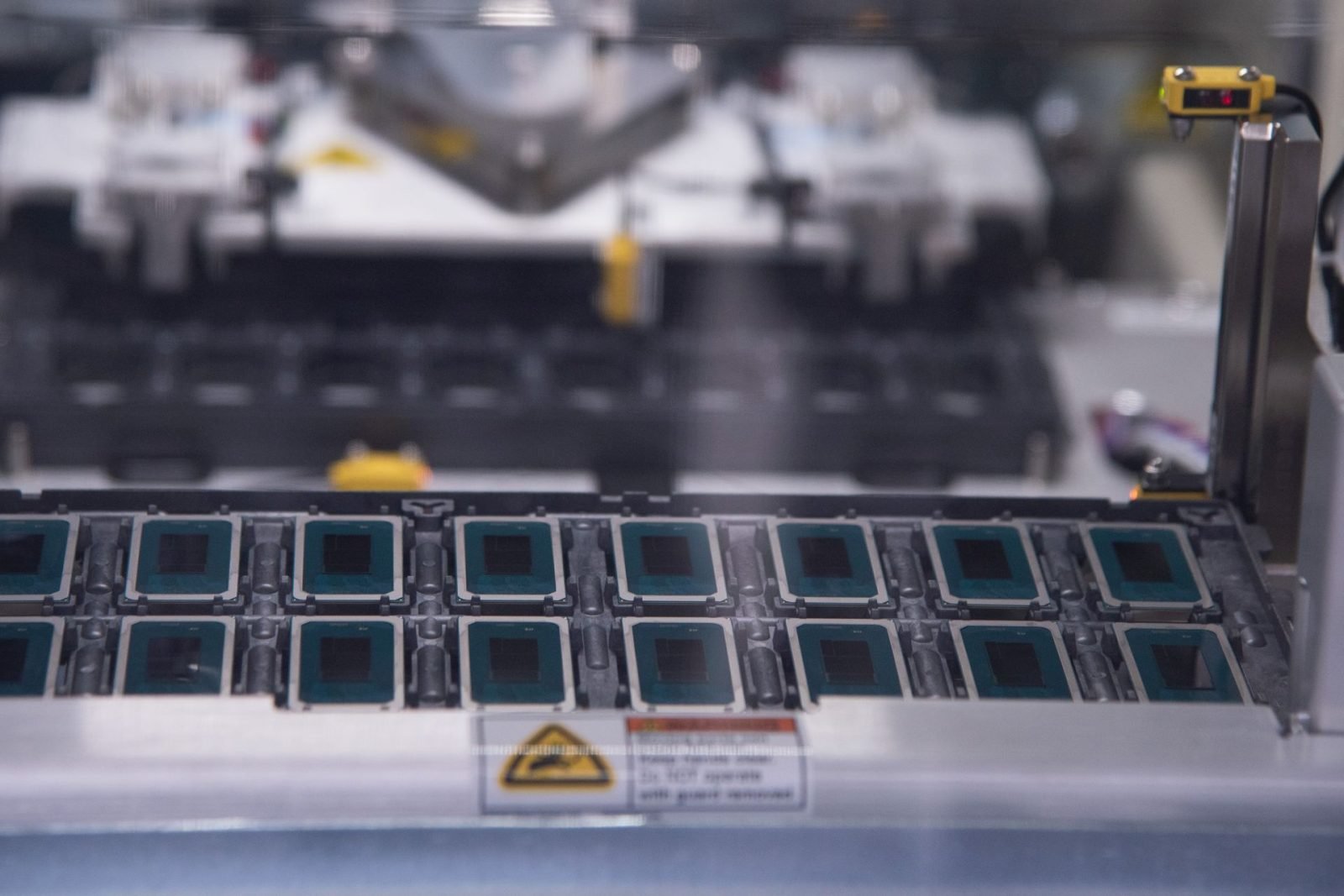
Następnym krokiem jest aplikacja żywicy epoksydowej. W zależności od kształtu “pokrywki”, spoiwo przyjmuje różny kształt okalający kość. Proces realizuje robotyczne ramię. Precyzja jest w tym przypadku dość istotna, bo ani odrobina zaaplikowanej żywicy epoksydowej nie może się znaleźć na kości. Jeśli zawiedzie jedno połączenie z tranzystorami, całość może zostać co najwyżej breloczkiem.
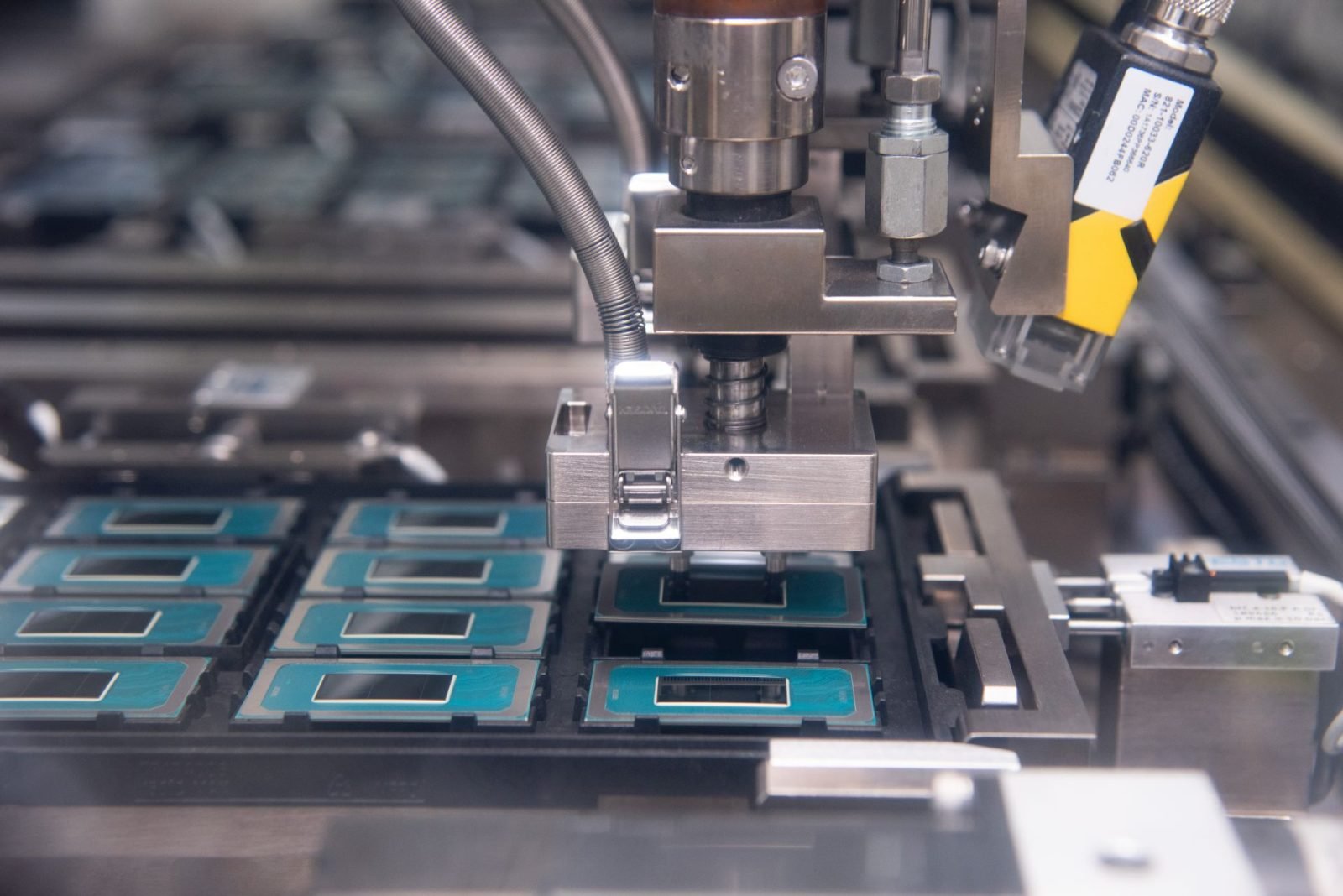
Po aplikacji żywicy następuje kolejny etap, czyli nałożenie interfejsu termicznego. W prostszym ujęciu możemy nazwać to po prostu “pokrywką”, której zadaniem będzie przyjmowanie oraz odprowadzanie ciepła. Jej powierzchnia jest jednolita i najczęściej wykonana z miedzi pokrytej warstwą niklu. To połączenie pozwala na efektywne rozprowadzanie ciepła nawet bez łączenia go z układem chłodzącym (choć ten poprawia wyniki).
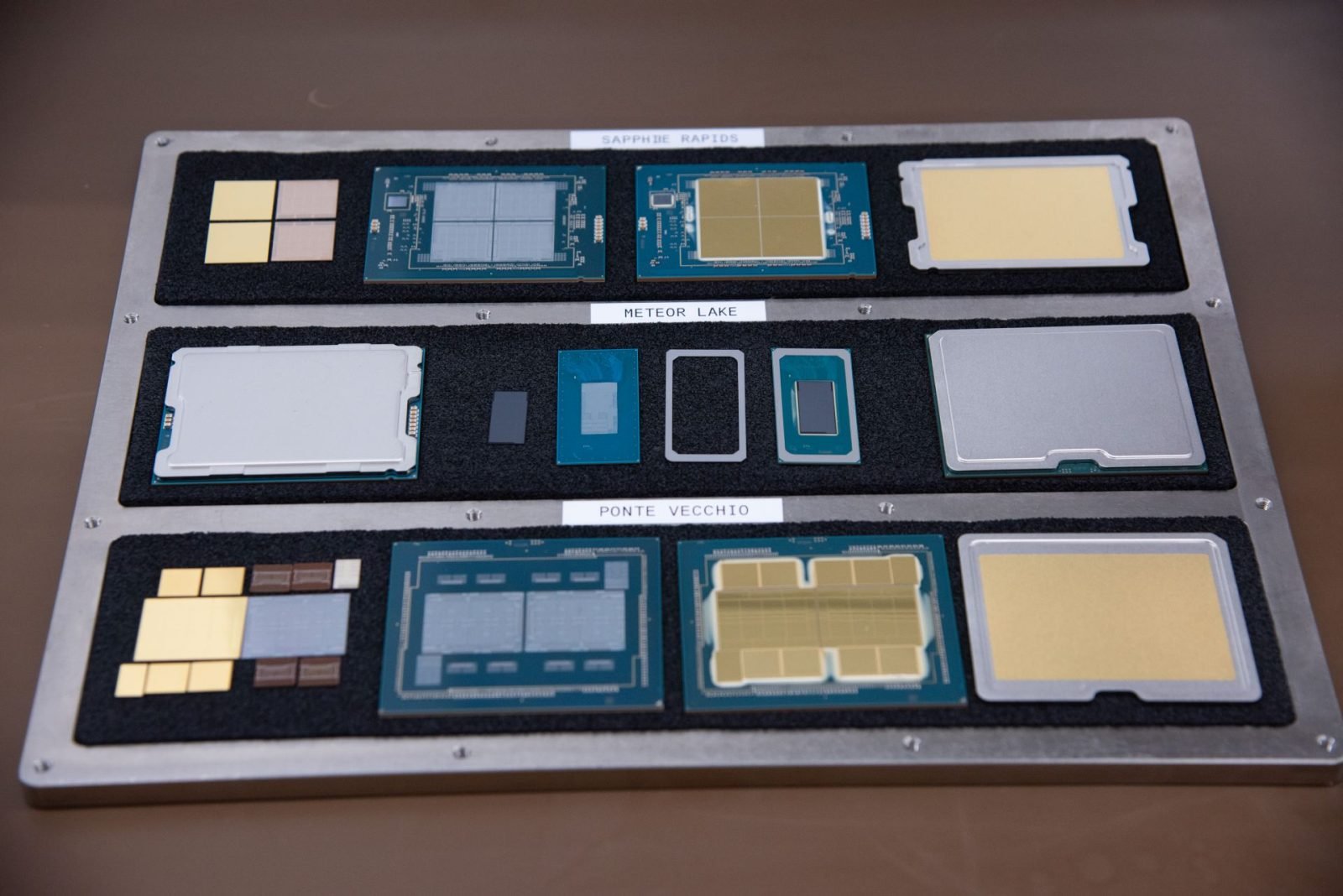
Następny proces to “wypalanie”. Procesor z pokrywką ląduje na półce, gdzie zostaje przekierowany na testy wysokiego napięcia oraz wysokich temperatur. To na tym etapie oddziela się wadliwe propozycje. Po wypalaniu przeprowadza się serię testów elektronicznych, gdzie sprawdza się działanie ścieżek elektrycznych oraz wszelkich funkcjonalności i trybów pracy, w jakich procesor brałby udział.
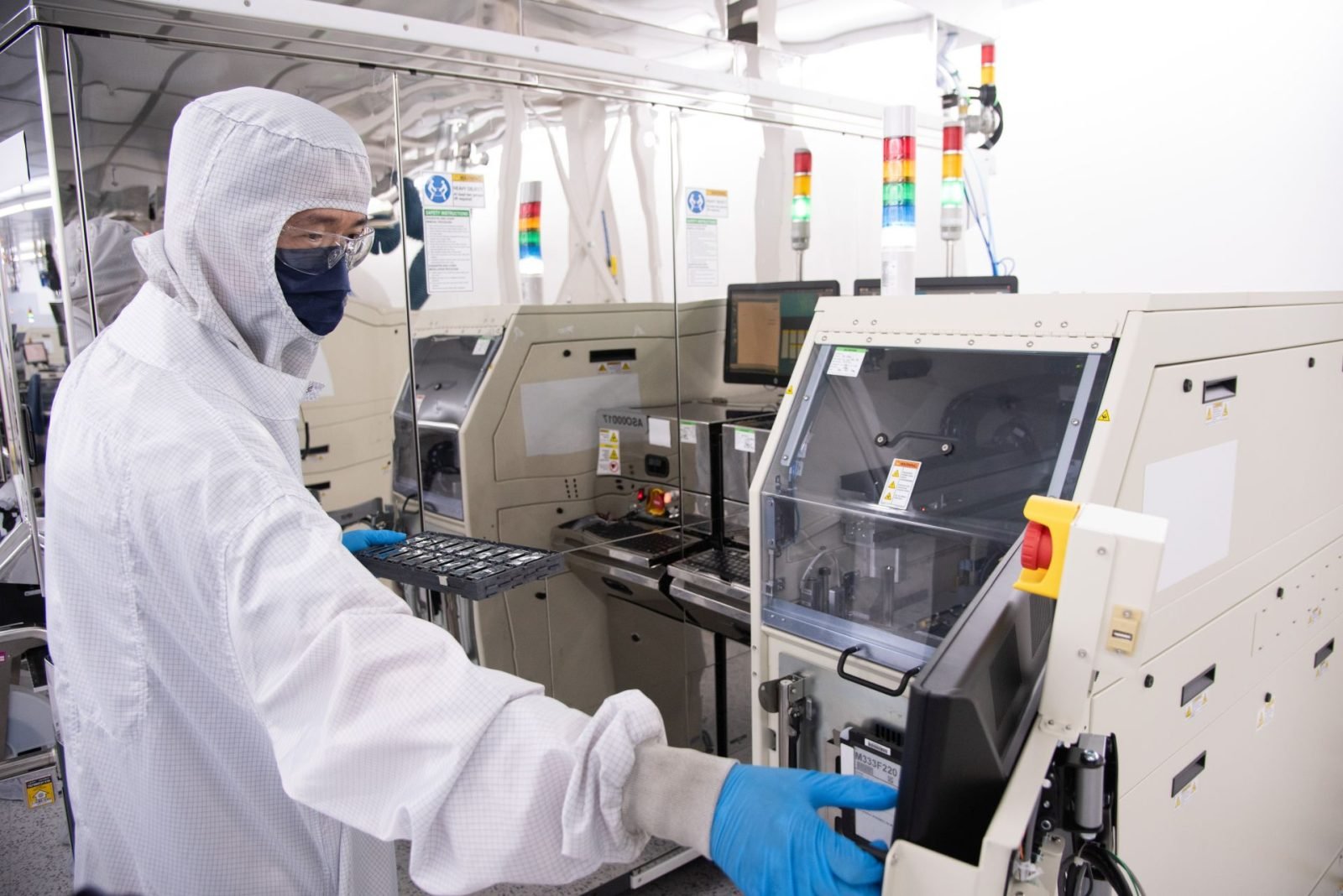
Na samym końcu odbywa się najbardziej konsumencka porcja testów, znana pod nazwą PPV – Processor Platform Validation. Procesory przenosi się do platform testowych, gdzie poddawane są one testom zbliżonym do korzystania z urządzeń w sposób konsumencki. Platformy te różnią się chociażby zastosowanym systemem – Windowsem, Linuxem oraz Ubuntu (tak, tego zbudowanego na jądrze Linuxa).
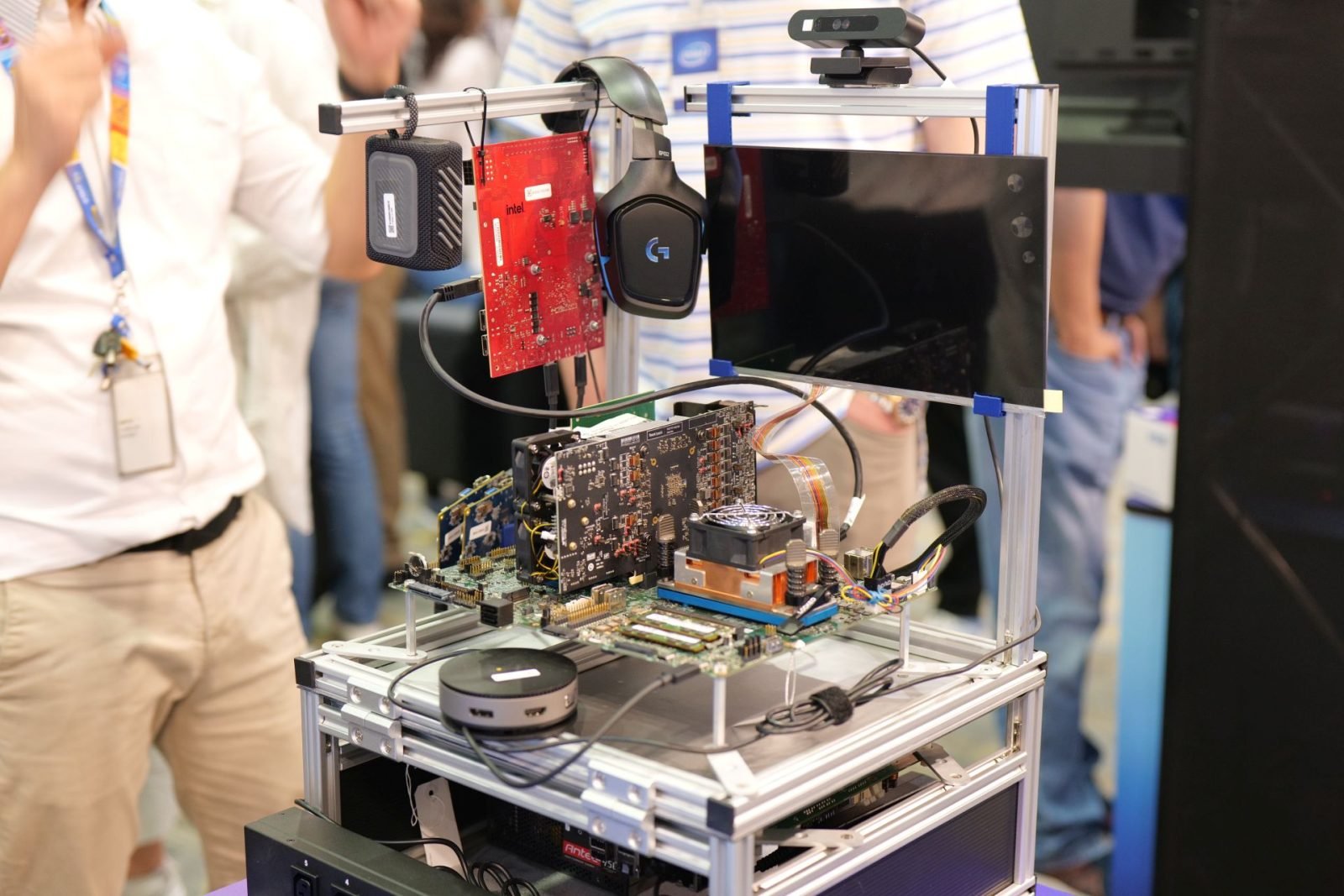
Takie zestawy testowe nieco przypominają nasze komputery. Różnicą jest chociażby to, że aby przetestować pełną funkcjonalność łącza USB, tworzy się niemal całkowicie odrębną płytę główną z portami i złączami wszelkiej maści – od slotu na karty Micro SD, przez złącze Ethernet (w końcu laptop może mieć przejściówkę do takiego zestawu), na zewnętrznym module Bluetooth kończąc. Takie same rozwiązania są na drugiej, większej płycie, ale tę mniejszą i tak należy skonstruować, by upewnić się, że przejście przez port USB nie wpłynie negatywnie na pracę jednego z modułów.
Czytaj też: Sztuczna inteligencja bez kobiet będzie przychylna mężczyznom?
Te rozwiązania to efekt pracy specjalistów z Intel System Integration and Manufacturing Services (SIMS). Ich platformy dotrą do Wrocławia w różnych formach, tak jak obecnie są rozsyłane do innych placówek, jak chociażby te w Wietnamie czy na Kostaryce. Wśród nich zarówno mniejsze rozwiązania dla testu procesorów do laptopów czy komputerów osobistych, jak i znacznie większe, o szerokości blatu sporego biurka, gdzie testuje się rozwiązania dla serwerów i centrów danych.
Kość na taśmie filmowej i diamentowe ostrza
Intel to zarówno architekt, jak i konstruktor swoich rozwiązań. Firma korzysta z usług i narzędzi kontrahentów, ale najważniejsze etapy procesu od początku do końca realizuje w swoich fabrykach. To daje jej nadzór, na jaki nie może sobie pozwolić chociażby współpracujące z TSMC Apple. Nie oznacza to z miejsca, że produkty Intela będą najlepsze na rynku, ale z pewnością pozwala na uniknięcie potknięć (choć też nie zawsze, czego przykładem są historie z przejściem na niższy proces litograficzny po 10nm).
Pamiętacie, jak wcześniej wspominałem o rolce z kośćmi, która przypomina taśmę filmową? Aby zobaczyć, jak zapełnia się ją kośćmi, udaliśmy się Kulim, gdzie znajduje się Die Prep Die Sort Operation – to w tym miejscu przetwarza się wielki wafel krzemowy na małe płytki. Wejście do tej przestrzeni wymagało od nas adekwatnego ubioru – nasza odzież została zabezpieczona ciuchami laboratoryjnymi osłaniającymi nasze kończyny. Do tego okulary ochronne, gumowe rękawice i klapki, które nakładało się na buty oraz pasek zabezpieczający przed wyładowaniem elektrycznym.
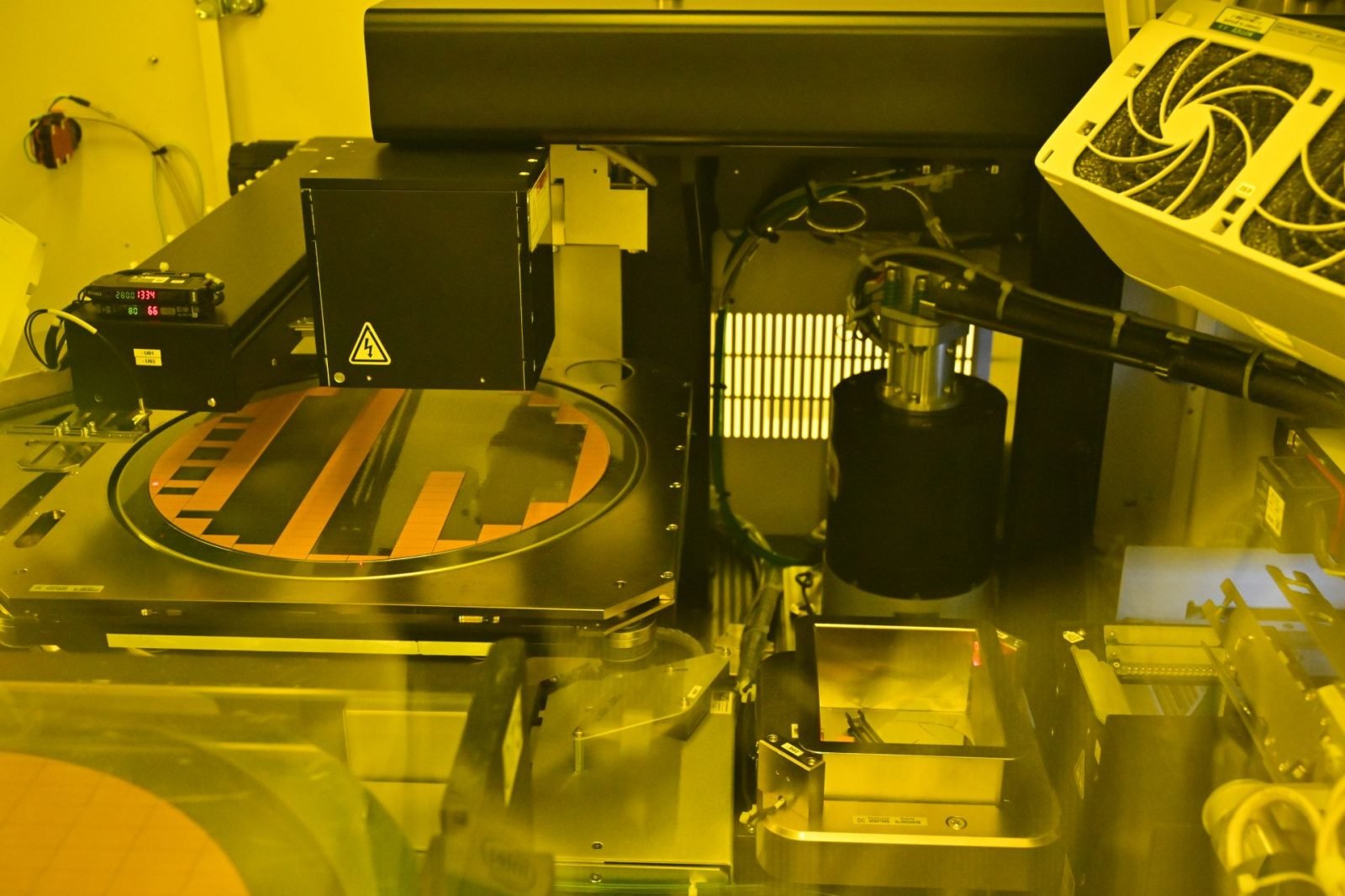
Cały proces odbywa się w fabrykach, gdzie znacząco ograniczono wpływ światła UV na wafle krzemowe. Stąd oświetlenie jest dojmująco żółte i przypomina kolorystykę części odcinków Breaking Bad. Nasz ruch w tej przestrzeni był odpowiednio sterowany przez pracowników, a o telefonach i aparatach ponownie mogliśmy zapomnieć.
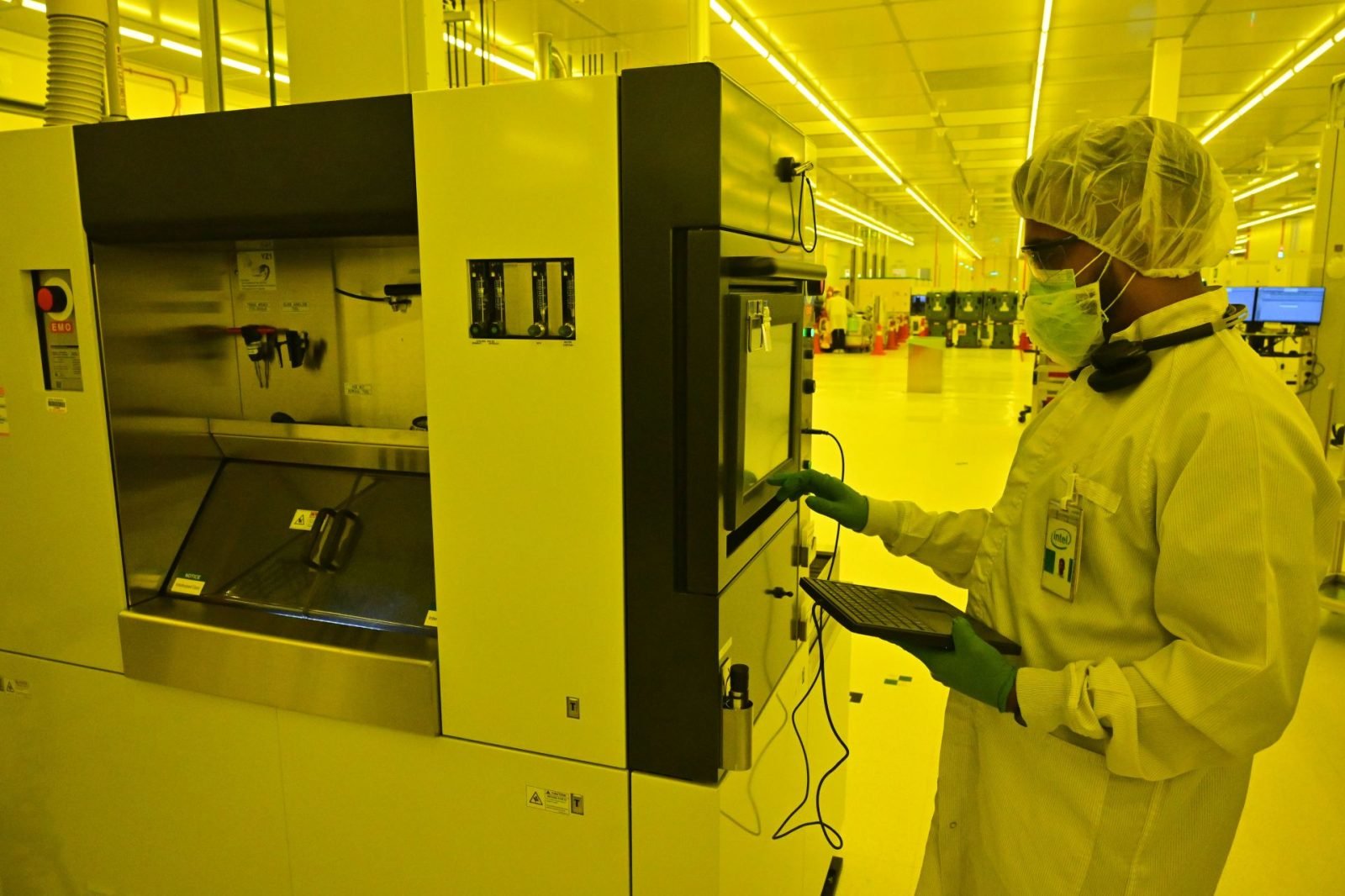
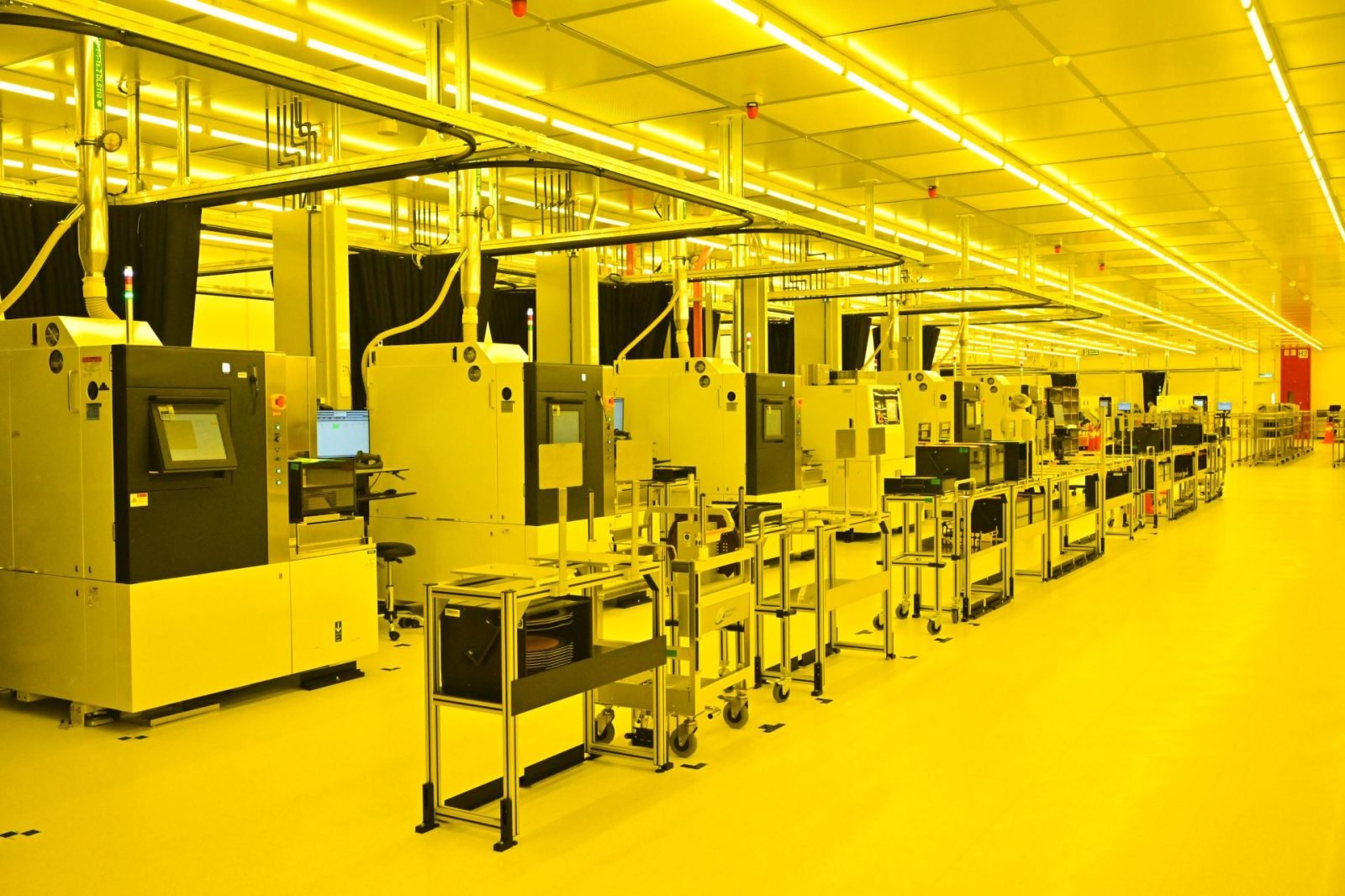
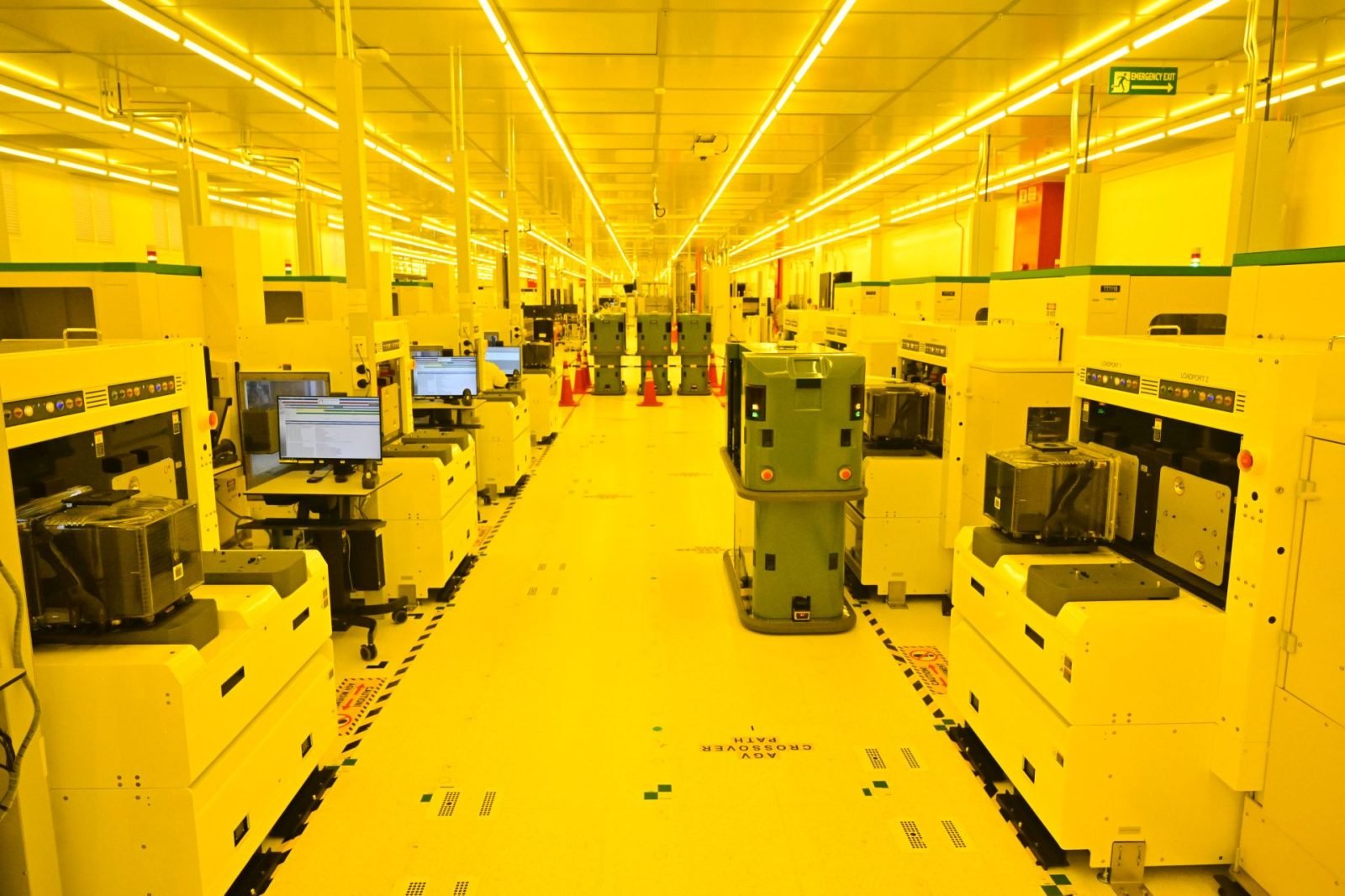
Pierwszy etap produkcyjny jest jednocześnie najbardziej skomplikowanym. Przygotowanie wafla o średnicy 300 milimetrów wymaga szlifowania oraz wykorzystania laserów i… diamentowych ostrzy nieustannie chłodzonych cieczą. Dlaczego wafli nie tnie się laserem? Metoda generowałaby zbyt duże ciepło i wbrew pozorom nie byłaby aż tak precyzyjna w krótkim czasie. Laser jest jednak potrzebny do cięć potrzebnych w mikroskali. Tymi bardziej widocznymi zajmują się okrągłe, diamentowe ostrza.
Wafel jest okrągły, a kości – najczęściej prostokątne. Co zatem dzieje się ze skrawkami spoza centrum koła? Tak naprawdę to nic – nie da się jeszcze przetworzyć ich, by miały cel przy ponownej produkcji. Odzyskuje się z nich jedynie cenne metale, a elementy na bazie krzemu lądują w koszu.
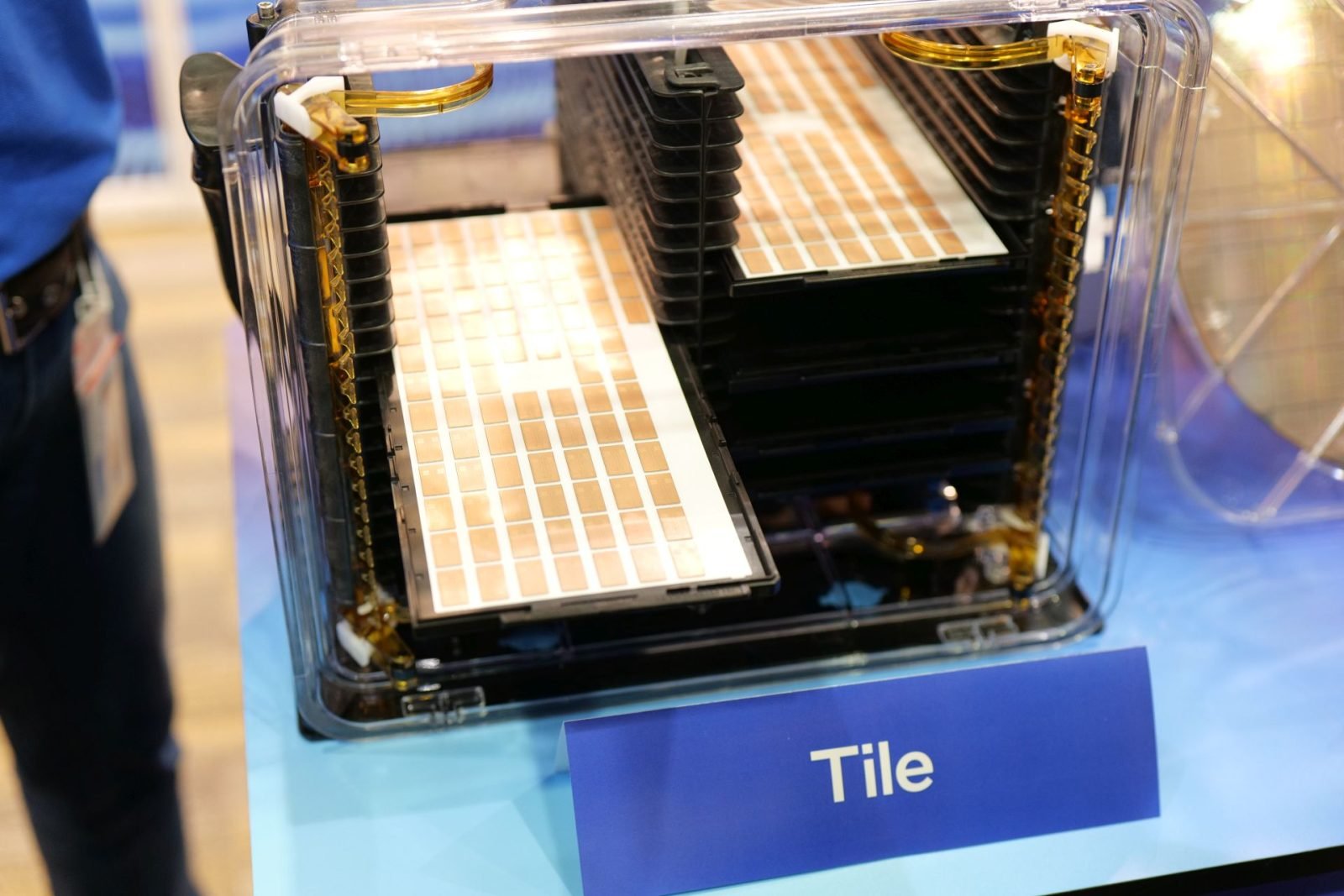
Tak wycięte kości umieszcza się na półce, którą wykonano z materiału o mikroskopijnych wgłębieniach, przez które kości zachowują swoją pozycję. Taki zestaw kości przewozi się do dedykowanych platform testowych. Każda z nich waży około 450 kilogramów, więc by umieścić je na odpowiednich półkach w przestrzeni testowej, niezbędny jest podnośnik, który generuje pod sobą poduszkę powietrzną. W rezultacie poruszanie nim nie należy do ciężkich i przypomina jazdę poduszkowcem. Niestety, Intel nie dostarczył zdjęć podnośnika, za to możecie zobaczyć same platformy testowe. Intel chwali się tym, że ich rozwiązanie w tej dziedzinie wyprzedza konkurencję pod względem skali oraz niezawodności.
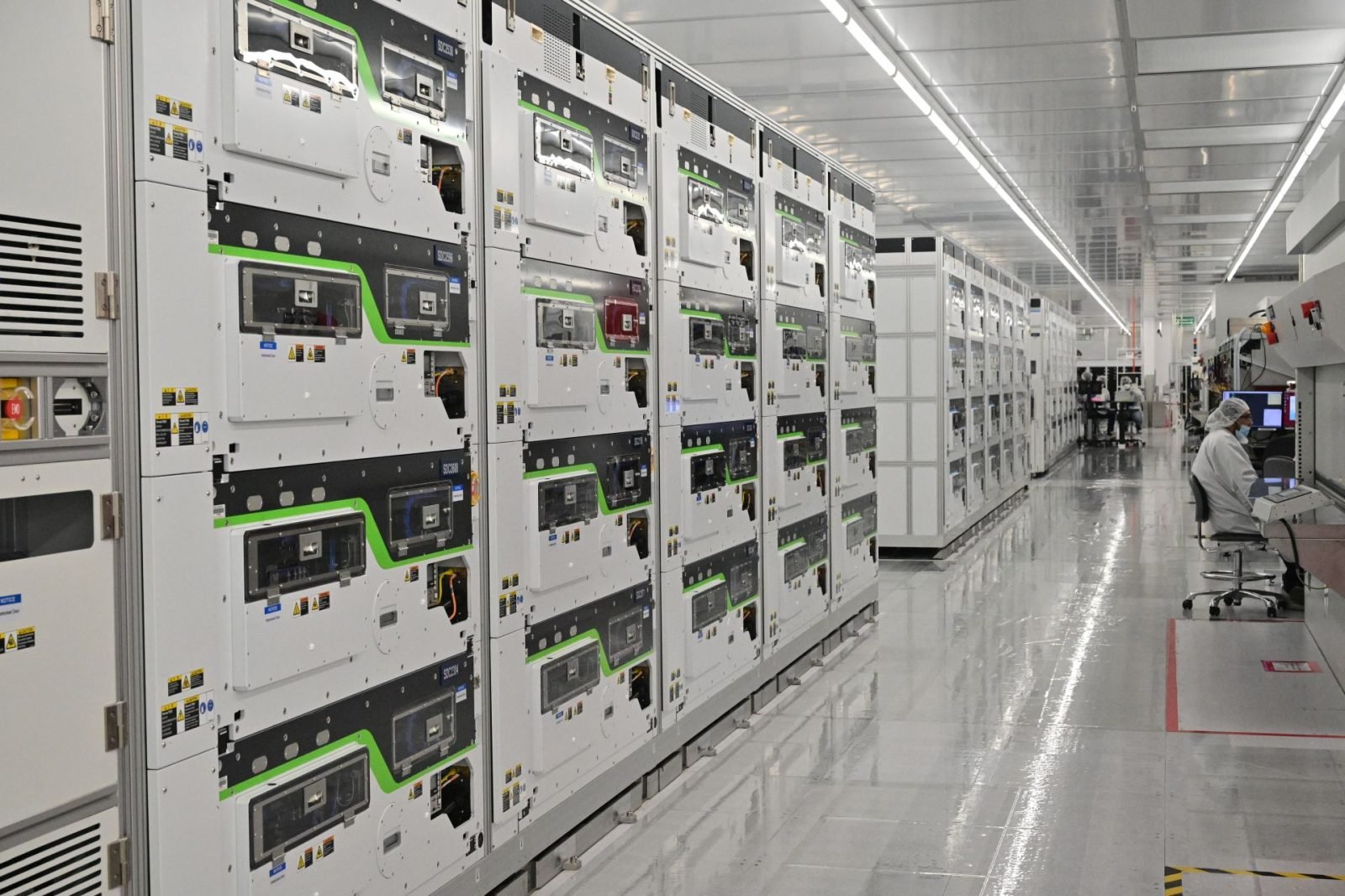
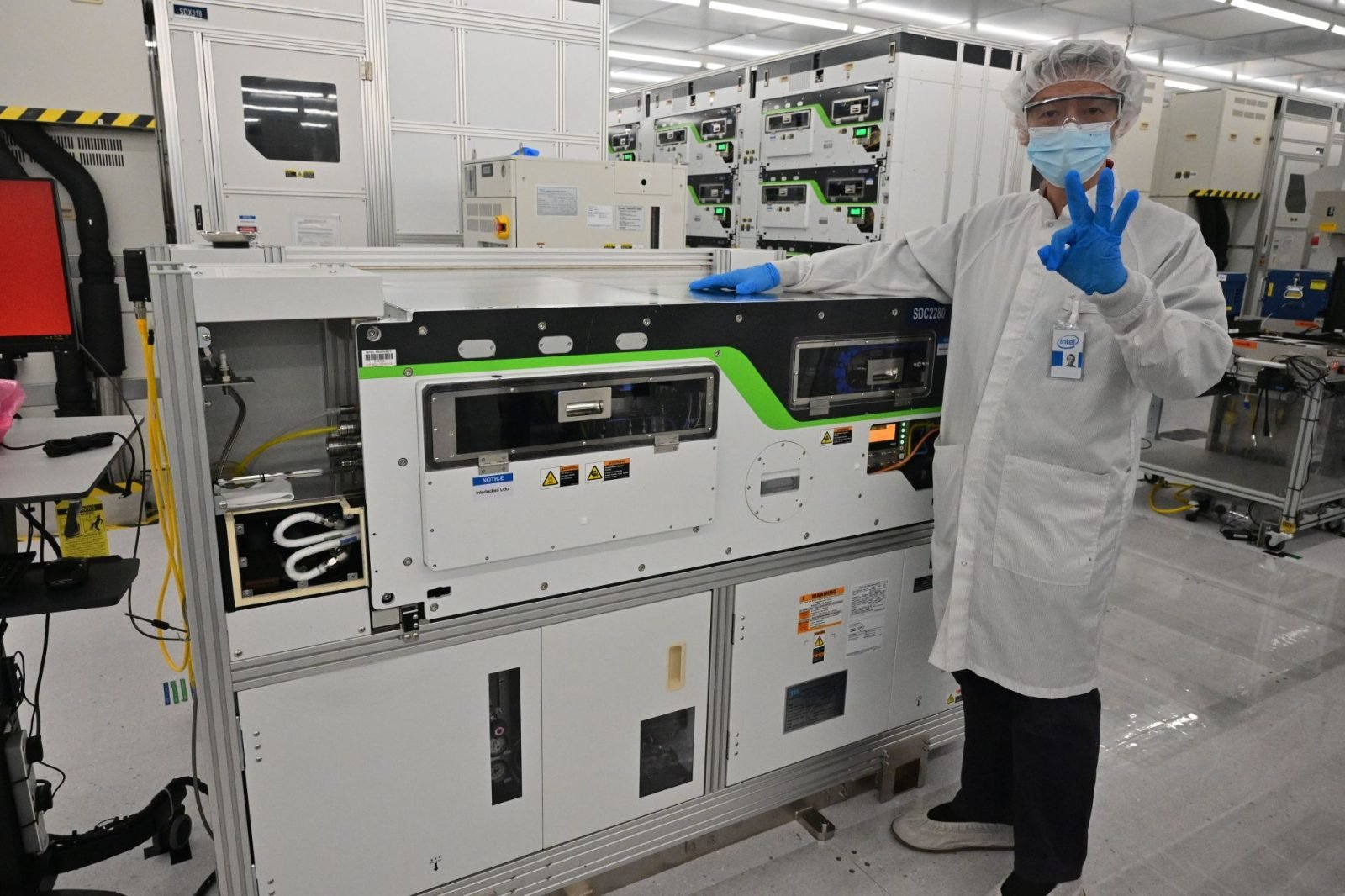
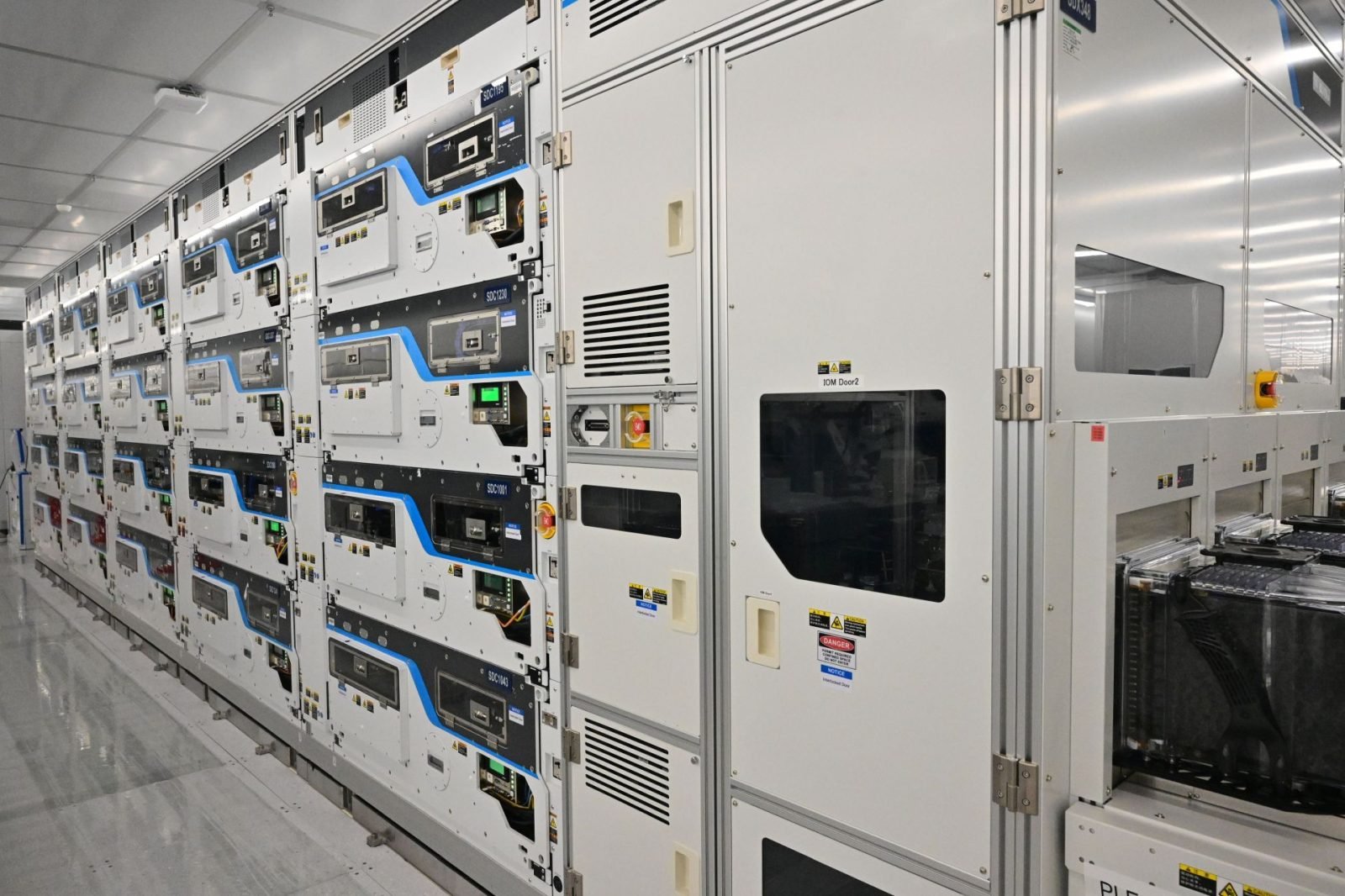
Po załadowaniu takiej platformy testowej do odpowiedniej szuflady rozpoczyna się działanie modułu sortującego. Każdą kość kładzie się na karcie testowej wyposażonej w tysiące igieł cieńszych od ludzkiego włosa. Taki układ scalony mierzy energię elektryczną w obwodach kości, by sprawdzić niezawodność i wykryć awarię.
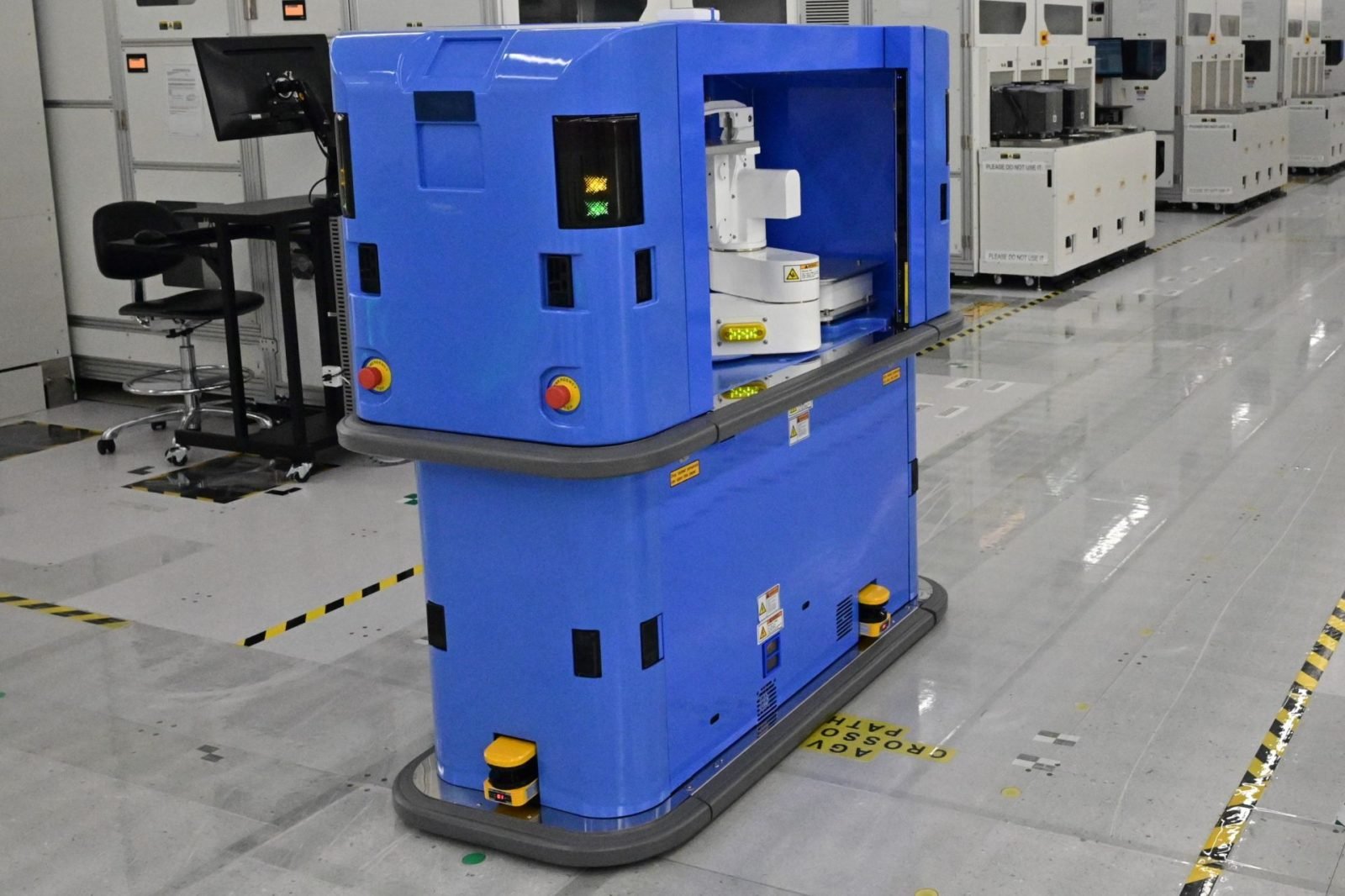
Po udanych testach kości są dostarczane do kolejnego modułu, gdzie nakłada się je na taśmę. Aby transport kości przebiegał jak najpłynniej, wykorzystuje się autonomicznie poruszające się roboty AGV (Automated Guided Vehicle). Zapamiętam je przede wszystkim ze względu na ich nieokiełznanie w obliczu spotkania dużej grupy ludzi oraz ze względu na charakterystyczną kompozycję, którą odtwarzają w celu uprzedzenia pracowników, że się przemieszczają. Takie przetestowane kości trafiają potem, w odpowiedniej temperaturze i z dala od światła słonecznego, do centrum składania i testowania, o którym pisałem wyżej.
Intel potrzebuje inwestycji, jeśli chce kontynuować swoją historię
Inwestycja Intela pod Wrocławiem ma spory sens, gdy weźmiemy pod uwagę bliskość sąsiedztwa z niemieckim Madgeburgiem i stosunkowo bliskie sąsiedztwo z istniejącą fabryką w Irlandii oraz powstającą w Izraelu inwestycją. Z perspektywy Europy może wydawać się, że to spory rozstrzał w odległościach, ale w praktyce to dystans o wiele krótszy niż ten dzielący produkcję procesorów w Arizonie z centrum składania i testów na Kostaryce. Intel musi mieć kilka ośrodków produkcji działających sprawnie także po to, by szybko reagować na zmiany w konsumenckiej technologii.
Przez ostatnie miesiące znaczną część medialnej uwagi zajmowały rozwiązania oparte o sztuczną inteligencję. W obecnej formie takie narzędzia jak ChatGPT, Stable Diffusion czy generator wypowiedzi Speechify pracują w oparciu o wymianę danych między jednostkami przetwarzającymi dane w chmurze, a naszym komputerem. Koszty przetwarzania treści przez mocne karty graficzne i serwery danych są spore, choć nikt nie chce tego otwarcie przyznać. A co, gdyby wyeliminować pośredników i powierzyć przetwarzanie danych jednostkom znajdującym się bezpośrednio w naszym komputerze?

Wszyscy dobrze wiemy, że algorytmy i modele sztucznej inteligencji są dookoła nas, a najczęściej odczuwamy ich obecność w smartfonach. To dzięki nim nieużywane aplikacje mogą być aktywne przez jakiś czas lub są kasowane z pamięci operacyjnej dość szybko, by zapewnić lepsze życie baterii. To dzięki nim otrzymujemy sugestie, które programy otworzyć i podpowiedzi podczas robienia zdjęć i nagrywania filmów dotyczące tego, jak je kadrować.
Później z tych zdjęć możemy usuwać obiekty, których nie chcemy w kadrze (takie rozwiązanie proponują między innymi Xiaomi oraz Google). Dlaczego nie przenieść tego potencjału do naszych komputerów, by bez potrzeby wysyłania danych poza obręb urządzenia mogły na przykład automatycznie generować napisy do montowanych filmów czy tworzyć gotowe pisma urzędowe lub grafiki do prezentacji?
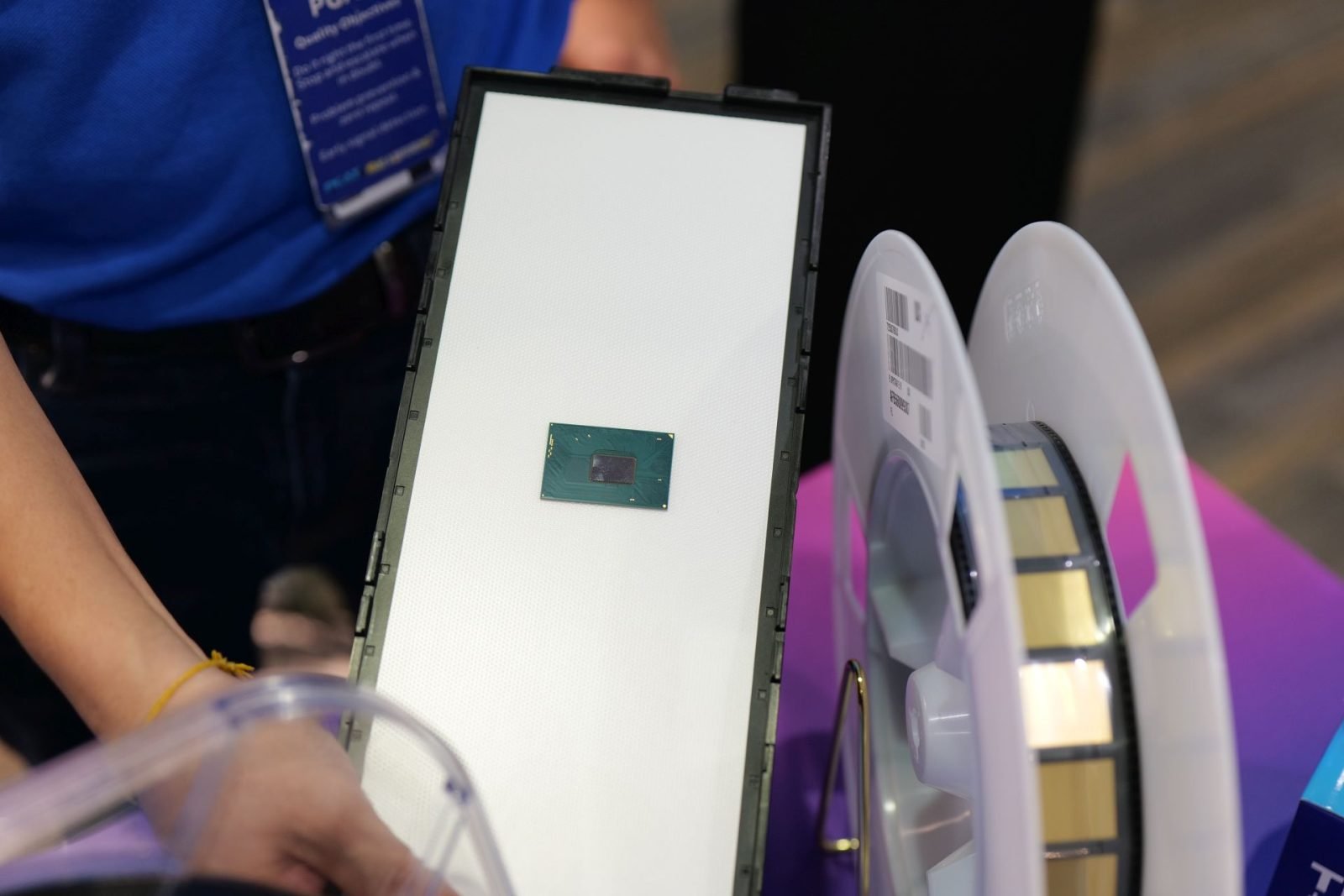
Niezależnie od tego, czy w tę stronę pójdzie Intel (a więcej o tym dowiemy się 18 września), rozsądnym jest, by firma przekierowała część swojej produkcji do Europy. Przedstawiciele Intela w ciekawych statystykach informowali chociażby o tym, że na ten moment składanie chipsetów oraz ich testy odbywają się w Europie dla 5% zapotrzebowania, a produkcja wafli krzemowych na starym kontynencie to 9% światowej produkcji Intela. W obliczu utrudnień, jakie serwował nam koronawirus czy agresja Rosji na Ukrainę, rozmieszczenie swoich fabryk i ośrodków testowych w Europie ma spory sens. Intel odważnie wchodzi w erę produkcyjną pod nazwą Intel 4 – oprócz powstającej fabryki w Madgeburgu podwójnie powiększy się przestrzeń kampusu w Leixlip w Irlandii, a pod Wrocław będą spływały setki tysięcy kości.
Zdecydowanie jest o co grać. Według przewidywań w 2030 roku przemysł produkcji układów obliczeniowych urośnie do biliarda dolarów. W końcu procesory, karty graficzne czy chipsety otaczają nas z każdej strony. Nie dziwi, że przeciętny Amerykanin z elektroniką spędza ponad 12 godzin dziennie. O ten czas warto walczyć nie tylko, gdy jest się firmą tworzącą media społecznościowe, ale i dostawcą podzespołów, dzięki którym nasz świat przeobraził się w ciągu kilku dekad w społeczeństwo technologiczne.